Columbia, S.C.’s atypical apprenticeship program is working, and here’s proof
When it rains, it doesn’t always pour. At least not at Columbia, South Carolina’s water resource recovery facility – even after a historic 1,000-year flood in 2015 and the wettest December on record three years later.
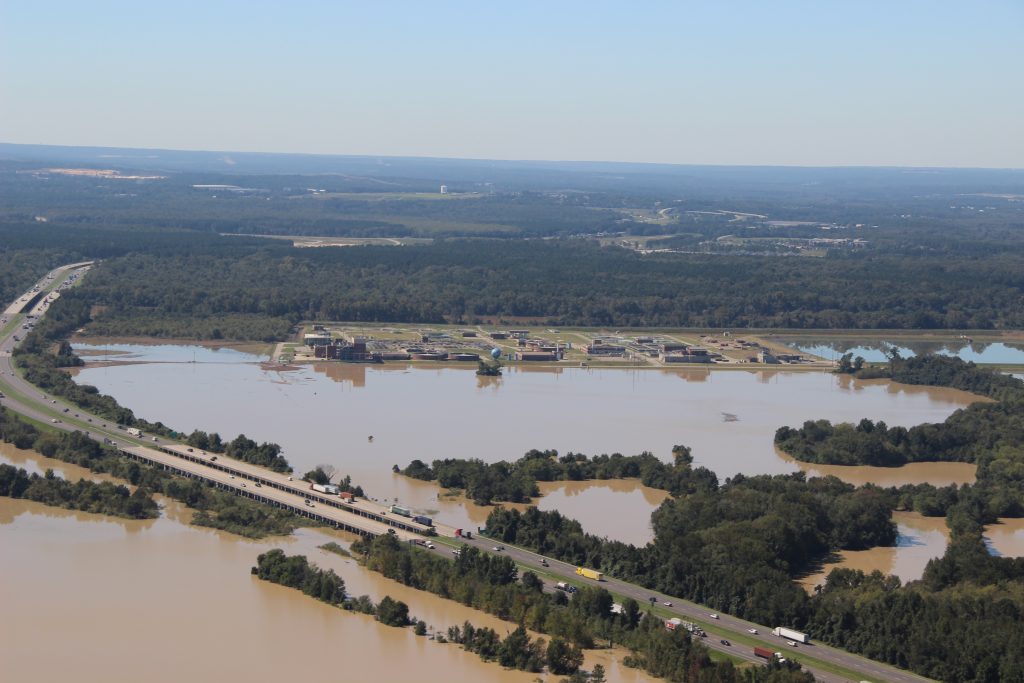
“During these periods, we were treating sustained flows that were 25 to 30% above design capacity every single day,” said David Wiman, superintendent for the city’s 60-mgd plant. “And every single day, the plant was well within regulatory limits.”
Wiman is proud of this accomplishment, but he is even prouder of the high-performing facility operators who made it possible. Their successes, he said, are due in no small part to the education and training many received through the not-quite-typical operator apprenticeship program Columbia Water created in 2012. A second program for maintenance staff kicked off in 2017.
Real-world learning for real-world results
Both programs are designed to meet a simple goal: to build a self-sufficient workforce from people who may have little or no experience, but display initiative, a strong work ethic, and a desire to learn.
“Typically, new operators are taught routines,” Wiman explained. “Learning the big picture may never come, or at the very least, it will be learned the hard way, through mistakes and plant upsets.”
Instead of focusing on routines, Columbia Water works instead to build big-picture thinkers by creating strong mentoring relationships, rotating apprentice operators throughout different parts of the facility, and training them to perform each task that keeps the treatment process moving.
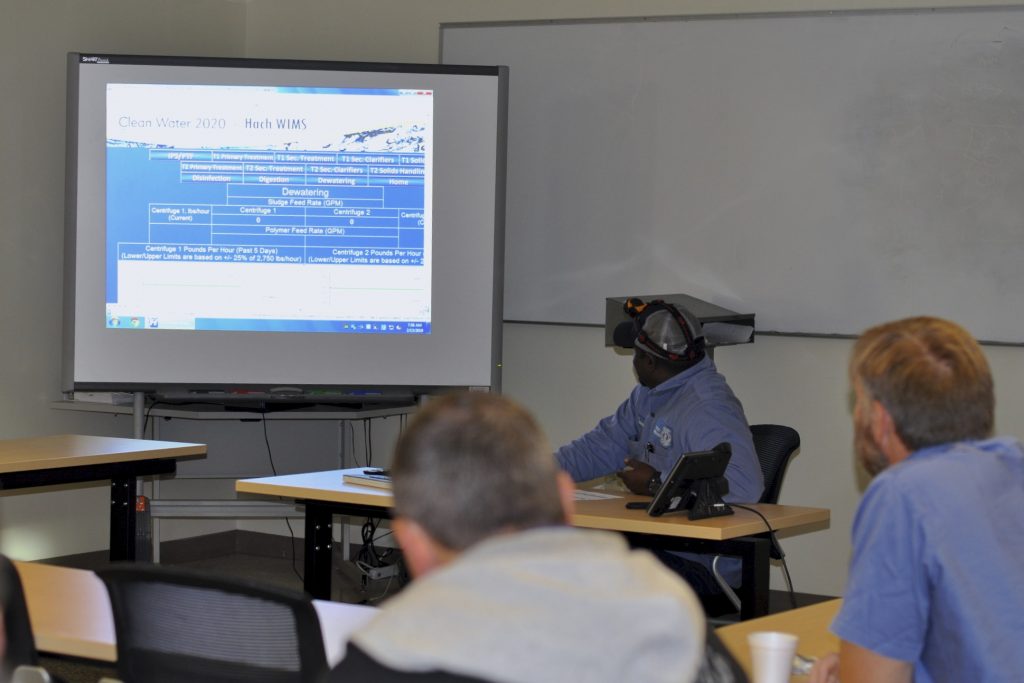
The goal is to prepare them to respond confidently and decisively to challenging situations, said Wiman, which he calls “an expectation of their workplace culture.”
When faced with a storm or other upset, “front-line workers must be able to react first and then communicate” to supervisors, said Wiman. “That communication….should go something like, ‘This happened. I contained the issue, identified the cause, and made these adjustments.’”
While a supervisor may make suggestions, Wiman explained, “we will never allow an event to continue unabated while someone waits to be told what to do.”
Testing competency
Of 48 operator apprentices enrolled since the program’s rollout in 2012, 46 have completed it. Obtaining certification requires not only passing competency exams, but also completing a competency walk-through with Wiman.
‘The walk-through loosely simulates a regulatory inspection,” he explained. Trainees receiving the lowest-grade certifications are asked what they would check during inspection rounds, while those seeking higher clearances are asked how they would respond to specific situations and facility conditions.
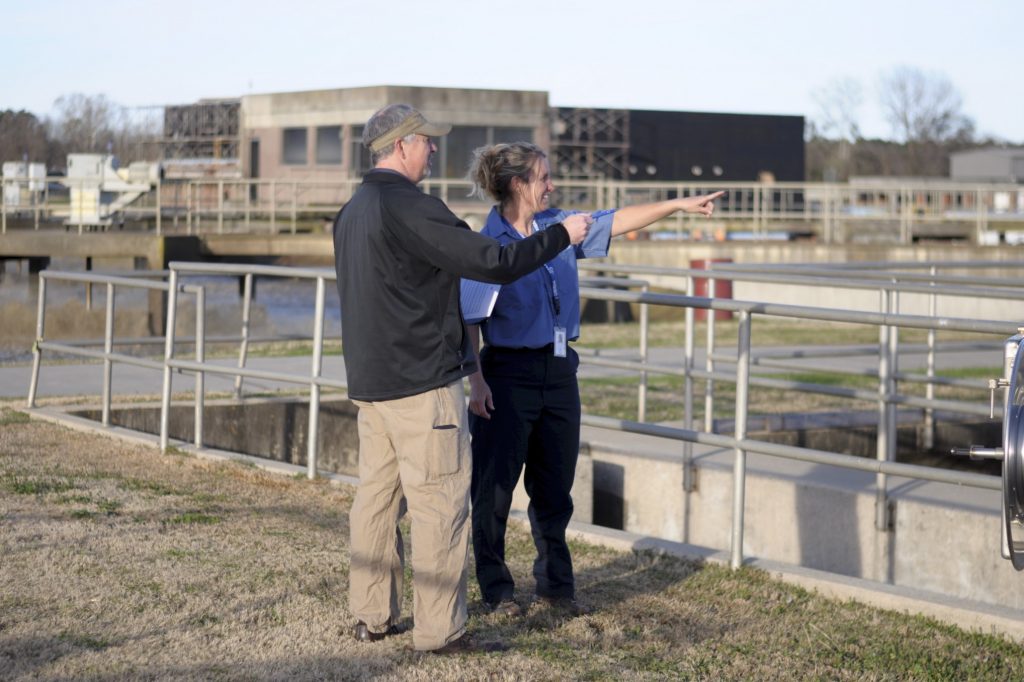
Columbia Water’s “big picture” approach appears to be working.
“I have operators with less than a year’s worth of experience that are farther along the learning curve than I was after my first six years,” Wiman said. Their expertise is demonstrated in the 20 awards the utility has earned during the past 7 years, including the inaugural Water Environment Federation (Alexandria, Va.) Water Heroes award. Columbia Water also fielded the first all-female Operations Challenge team at WEFTEC 2018. Also of note: the city’s water effluent quality is also on the rise.
As the apprentice program continues to draw new people to clean water careers, Wiman’s philosophy remains rooted in “guiding and teaching, not micromanaging.”
“This is not an exact science,” said Wiman, “but we’ve gotten pretty good at it.”
— Mary Bufe, WEF Highlights